Blasting & Drilling
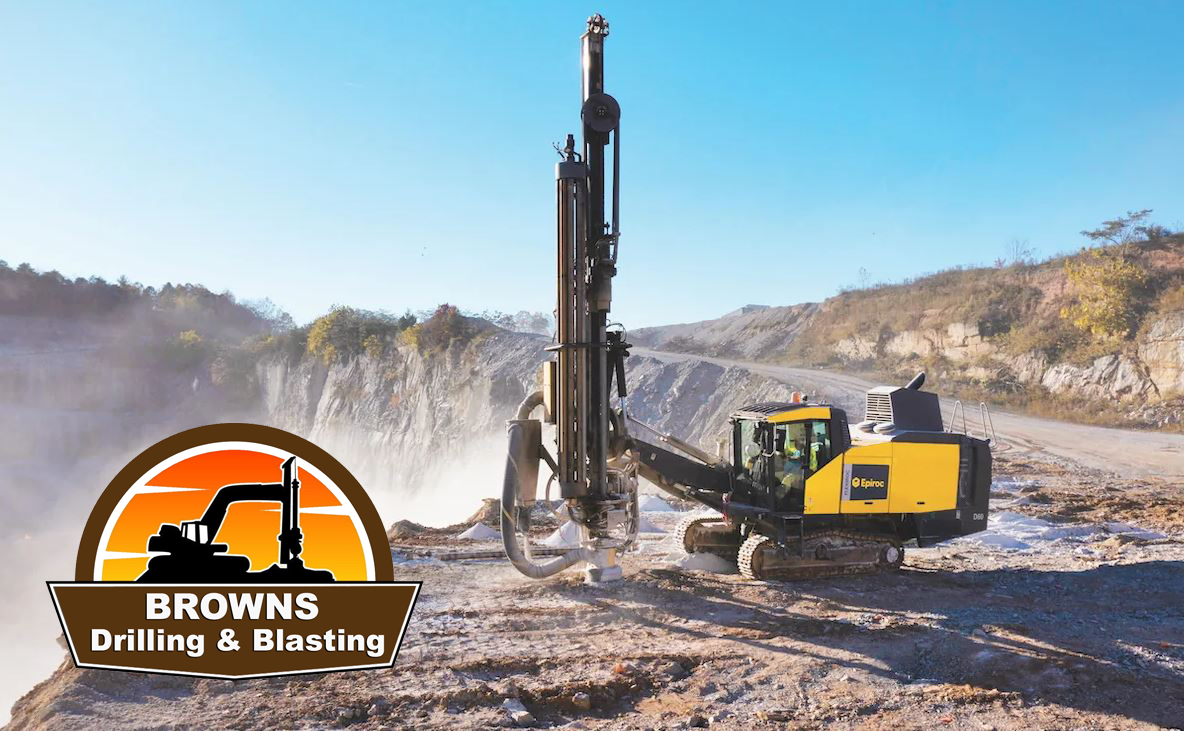
What is drilling and blasting?
Drilling and blasting is the controlled use of explosives and other methods, such as gas pressure blasting pyrotechnics, to break rock for excavation. It is practiced most often in mining, quarrying and civil engineering such as dam, tunnel or road construction. The result of rock blasting is often known as a rock cut.
Drilling and blasting currently utilizes many different varieties of explosives with different compositions and performance properties. Higher velocity explosives are used for relatively hard rock in order to shatter and break the rock, while low velocity explosives are used in soft rocks to generate more gas pressure and a greater heaving effect. For instance, an early 20th-century blasting manual compared the effects of black powder to that of a wedge, and dynamite to that of a hammer.[1] The most commonly used explosives in mining today are ANFO based blends due to lower cost than dynamite.
What are the benefits of drilling and blasting ?
The main benefits of drilling and blasting technology are that it is very cost-effective, offers great versatility, and is suitable for most ground conditions.
It can also be used to create openings with a more predictable shape than those made by mechanical excavation systems.
Moreover, due to the short cycle times, drilling and blasting can be used for large earth moving projects, such as the construction of underground tunnels and highways.
Finally, blasting technology can also be used to break up rock into smaller pieces that can then be moved, crushed or milled.
What does the process of drilling and blasting entail?
The drilling and blasting technique consists of the drilling of boreholes in the rock, the placing of explosives and blasting to properly fragment the work section.
The typical cycle of excavation by blasting is performed in the following steps:
1. Drilling
As the word suggest, this step involves drilling blast holes and loading them with explosives.
During this step, jumbo machines are used to drill the holes where the explosives will be charged.
Jumbo machines are have three drilling arms and an operator tower. These tools run by electric cable; a hose brings water to pneumatic drills allowing for the drill bits both hammer and rotate. These drill holes can be between 2.4-3.6 metres long.
2. Explosive Charging
The boreholes are filled with explosives, detonators are attached to the explosive devices and the individual explosive devices are connected to one another. Some of the explosive devices commonly used include dynamites, hydro-gels, emulsions and ANFO (Ammonium Nitrate Fuel Oil).
The process of charging equipment is typically mechanized for safety purposes. Charging explosives this way ensure that explosives are safely charged into the boreholes.
In terms of safety, civil and structural engineers can now monitor hazardous areas remotely thanks to remote sensing technology.